Tower crane electrical maintenance and troubleshooting
Publication Date: 2019-07-25
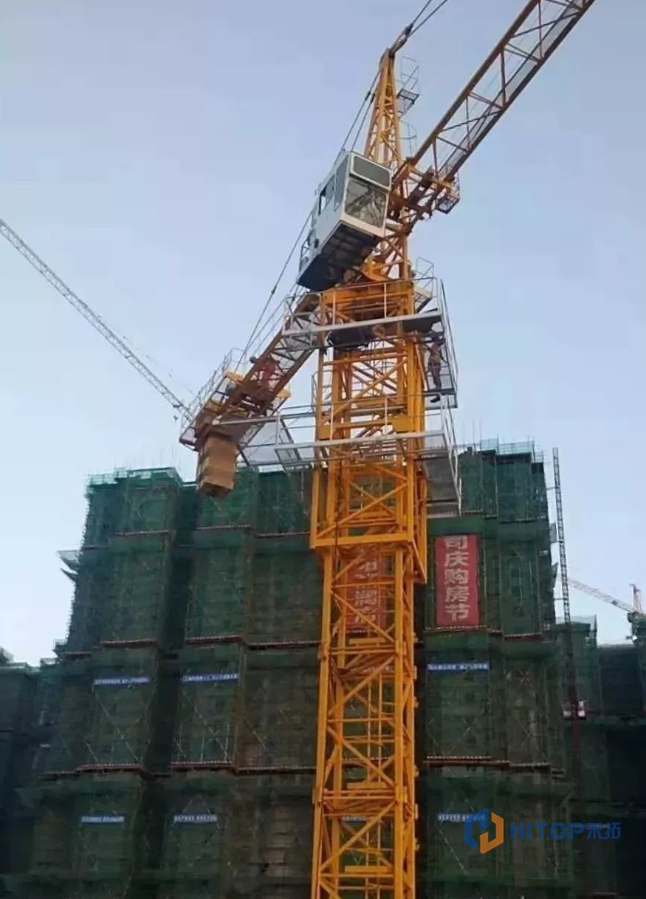
1. Maintenance and maintenance points
In the daily use of the tower crane, in the absence of maintenance, the mechanical system often has phenomena such as loud noise and overheating; its electrical system fault is difficult to observe directly, and there is no obvious precursor. The sudden failure of the tower crane is mostly in the electrical system, which requires us to do the maintenance and maintenance of the electrical system in advance to prevent electrical failures.
(1) Lightning protection
Lightning strikes can cause serious damage to the electrical system of the tower crane. A K80 tower crane at a construction site was not completely powered off due to lightning weather, causing the running inverter and the torque limiter main unit to burn out. The highest position of the tower A-frame must be equipped with a lightning receptor (lightning rod), a down conductor and a grounding body. The bottom of the tower crane (walking tower crane track) must be grounded in strict accordance with the regulations. When the lightning occurs, the whole machine must be powered off and cannot continue to work.
(2) Rainproof
According to experience, after the rain is the multi-period of electrical failure of the tower crane. The construction site generally does not stop construction when the rain is not particularly large, and the tower crane is also required to operate on rainy days. The motors of several mechanisms of the tower crane are installed in the open air. If rainwater enters the motor, the grounding trips lightly, causing a short circuit and burning the motor. Therefore, under the condition of ensuring smooth ventilation, the electrical cabinet and motor of the tower crane should adopt rainproof measures, such as adding rain cover.
(3) Pollution prevention
Generally, the construction site is dusty, and the accumulation of dust on the electrical components of the tower crane may result in poor contact. Therefore, according to the specific conditions of the site, the main electrical components such as cable connectors, contactors and circuit breakers should be periodically dusted after power failure.
The control cable of the lubrication part on the tower machine is easy to be stained with oil. If it is not cleaned for a long time, the rubber on the outer surface of the cable will be corroded, exposing the bare wire, causing short circuit and grounding. Therefore, after the lubrication and maintenance, the cable should be inspected for oil stains. If it is, it should be wiped clean with cotton yarn.
(4) Regular tightening
The tower crane vibrates greatly during operation, which tends to cause the bolts to loosen and the thread ends to fall off. Therefore, it is necessary to tighten the cable joints and the connecting bolts at various parts on a regular basis. For example, a tower crane has a phenomenon of lifting heavy objects, but the inverter has no alarm and all electrical components are working normally. After inspection, the reason is that the rotary encoder connecting bolt on the hoisting motor is loose, causing a deviation in the speed feedback.
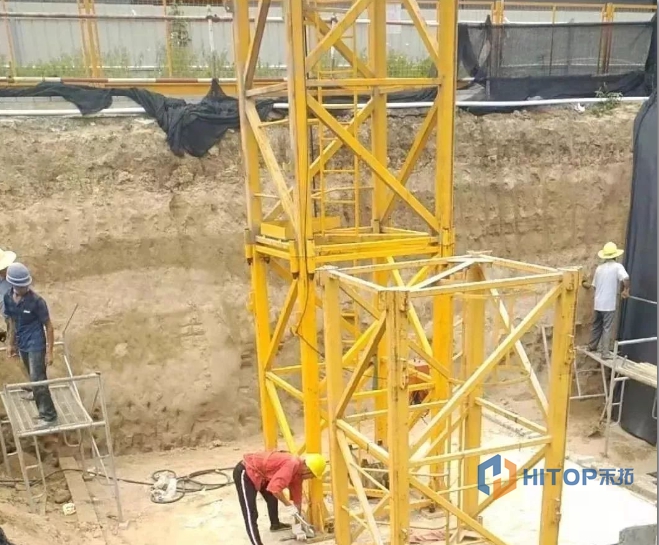
2. Common faults and troubleshooting methods
After an electrical fault occurs, it is first necessary to determine which part of the problem is present. The problem of one mechanism will not affect the operation of other institutions. If several organizations cannot operate at the same time, it can be judged that it is the main power supply, PLC or some components on the linkage table. Something went wrong.
The rotary electrical system of a large tower crane is basically a variable frequency control, and its fault manifests itself in a fault code on the display panel of the frequency converter. Inverter faults can be divided into two types, namely external faults and internal faults. The most common one is the external fault. The external end of the inverter is connected to the motor and the resistance box, and the other end is connected to the control system PLC.
The order of troubleshooting should be simple to complex. Check the motor and resistor box first, then check the PLC and related contactors and circuit breakers.
Electrical faults are concealed, and fault detection and troubleshooting can be reversed. Common faults and troubleshooting methods are described below.
(1) Sparks appear on the power transmission trip or the main power supply terminal of the inverter
Disconnect the power cord and check if the inverter input terminal is short-circuited. Is the DC-side terminal P and N of the inverter intermediate circuit short-circuited. If shorted, the cause may be damage to the rectifier or short circuit in the intermediate circuit.
(2) Power transmission without display
Disconnect the power cord and check if the power supply has a phase loss or open circuit. If the power supply is normal, then check the power supply again to check whether the DC side terminals P and N of the inverter intermediate circuit have voltage. If the above check is normal, judge the internal power switch of the inverter. damage.
(3) No output when starting up, the motor does not start
Disconnect the output motor wire, turn it on again to observe the input frequency displayed on the inverter panel, and measure the AC output terminal. If it is normal, the cause may be the inverter startup parameter setting or the operation terminal wiring error, or the inverter part is damaged or the motor is not connected to the inverter correctly.
(4) The inverter stops outputting
Excessive motor voltage, excessive current, overheating, and poor grounding can cause the drive to stop output.
If the voltage is too high, check if the grid voltage is too high, or if the motor load is too large. If the motor load is too large and can only be stopped in a short time, you need to purchase the inverter with brake function and configure the corresponding system. Dynamic resistance.
If the current is too large, first check if the motor load is too large and adjust the inverter parameters appropriately. If the adjustment does not work, it may be that the inverter is aging or damaged.
Motor overheating may be due to excessive ambient temperature exceeding the allowable limit of the drive. In this case, check if the cooling fan is running or check if the motor overheat protection is normal.
(5) No action in rotation
If there is no action, please observe the external wiring first. If the wiring is normal, use a multimeter to check the resistance of the resistor box and the motor terminal to determine which part is shorted or grounded.
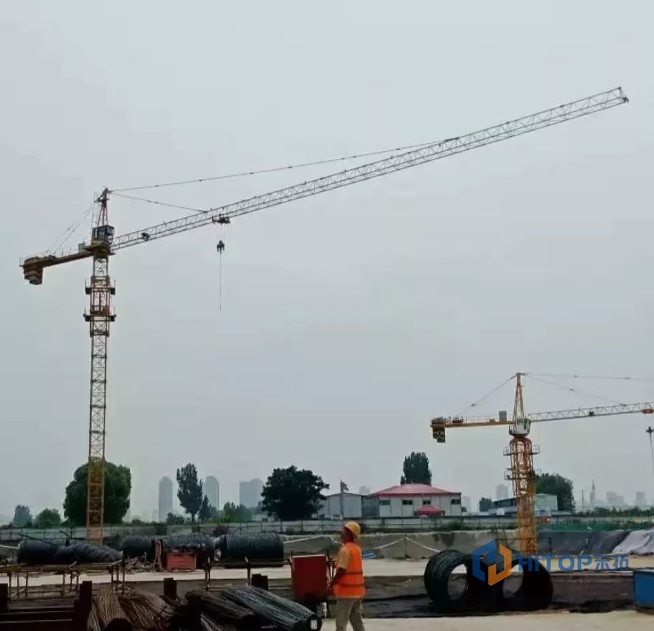